Plate rolls are machines used in Metal Rolling Technology to bending of metal sheets and shape metal plates by rolling them into cylindrical or conical shapes.
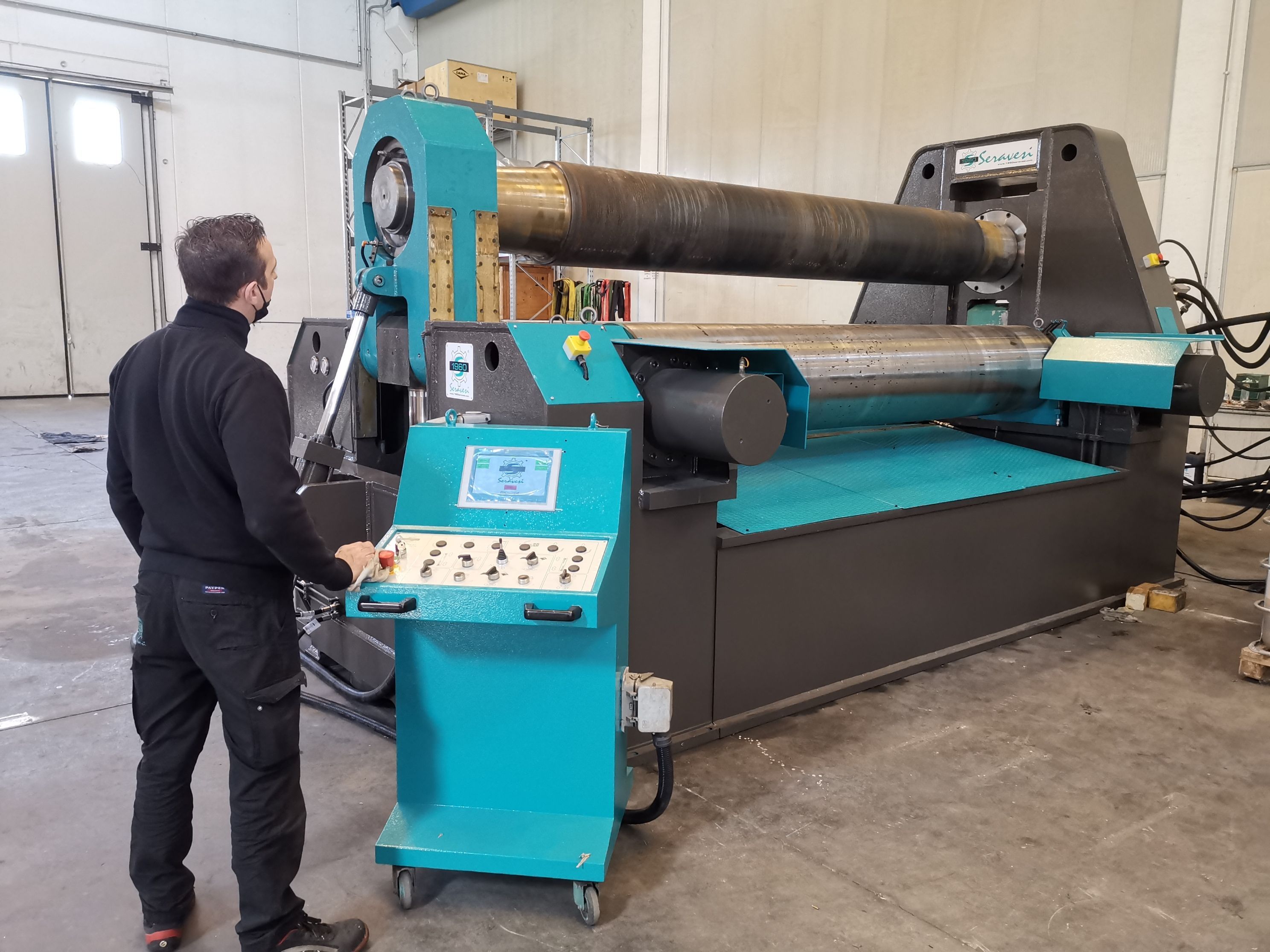
In the world of metal fabrication, the ability to bend and shape metal with precision and efficiency is crucial. One of the most widely used machines in this realm is the plate roll, also known as a plate bending machine or plate rolling machine. These machines are foundational to many industries, including shipbuilding, aerospace, energy production, construction, and heavy manufacturing. Whether you’re rolling cylinders, cones, or complex curves, plate rolls are indispensable tools in achieving accurate, repeatable results. Explore the fundamentals and benefits of plate rolls, how they work, where they are used, and how to choose the right one for your specific needs.
- What is a Plate Roll?
- How Does a Plate Roll Work?
- Key Advantages of Plate Rolls
- Applications of Plate Rolls
- Choosing the Right Plate Roll
What is a Plate Roll?
A plate roll is a mechanical or hydraulic device used to bend and shape flat metal sheets into curved forms such as cylinders or cones. These machines apply force through a set of rollers that gradually shape the material to a specific radius.
Types of Plate Rolls
There are several types of plate rolls, each offering different capabilities:
-
3-Roll Plate Rolls: These machines have one top roll and two bottom rolls. They are versatile and can handle medium to heavy plate bending.
-
4-Roll Plate Rolls: This type adds an additional bottom roll, providing superior control, pre-bending capability, and ease of use. They are often preferred for high-volume or automated operations.
-
2-Roll Plate Rolls: Less common, these are used for light-duty operations or where high precision is needed on thin materials.
-
Variable Geometry Plate Rolls: Designed for very thick plates, these adjust the lower rolls to apply different forces, optimizing the bending process for heavy-duty applications.
Each of these machines serves a distinct purpose and comes with its own strengths depending on the application.
How Does a Plate Roll Work?
The Bending Process
At its core, a plate roll works by passing a flat metal sheet through a set of cylindrical rollers, each exerting pressure to force the material into a curve. The bending process usually includes:
-
Feeding the Material: The flat plate is loaded into the rollers.
-
Pre-Bending: One of the rollers presses the plate edge to reduce flat spots.
-
Rolling: The plate is fed through the rolls repeatedly while the rollers gradually apply pressure, causing the material to curve into the desired shape.
-
Finishing: The shaped plate is released once the required radius is achieved.
Roll Movement and Control
In modern machines, especially hydraulic and CNC-controlled plate rolls, the position and pressure of each roller can be precisely controlled. CNC systems allow for automated processes, higher accuracy, and repeatable quality in batch production.
For example, a 4-roll system offers simultaneous control over pinching, bending, and plate feeding, which not only increases efficiency but also reduces manual handling.
Key Advantages of Plate Rolls
Investing in a plate rolling machine brings numerous advantages to manufacturers and fabricators. Here are some of the most significant:
Plate Rolls Versatility
Plate rolls can handle a wide range of materials and thicknesses, from thin aluminum sheets to thick steel plates. This makes them suitable for countless applications, including tanks, pipes, structural components, and pressure vessels.
Plate Rolls Precision and Repeatability
Modern plate rolling machines, especially CNC-controlled ones, offer high precision. Pre-bending capabilities eliminate flat ends, and digital controls allow users to replicate the same curvature across many parts with exceptional consistency.
Plate Rolls Efficiency
With a plate roll, large-scale bending jobs can be completed in minutes. 4-roll plate rolls, in particular, allow for one-operator use, faster setup, and reduced waste, maximizing productivity.
Plate Rolls Reduced Material Waste
By enabling precise control over the bend, operators can avoid trial-and-error mistakes. This minimizes wasted material and saves costs, especially when working with expensive metals.
Plate Rolls Safety
Compared to manual bending processes, plate rolls offer improved safety features, including emergency stops, pressure sensors, and guarded moving parts. This protects operators and ensures compliance with workplace safety standards.
Applications of Plate Rolls
Plate rolls are used across a wide array of industries, each requiring different shapes, sizes, and materials. Some of the most common applications include:
Oil and Gas Industry
In this sector, pressure vessels, storage tanks, and pipelines require precise curvature. Plate rolls are instrumental in fabricating thick-walled steel components that must withstand extreme pressures and environmental conditions.
Shipbuilding and Marine
Large, curved plates are integral to ship hulls, bulkheads, and superstructures. Plate rolls are used to form long steel plates into curved panels that make up the framework of ships and submarines.
Aerospace and Aviation
Aircraft components such as fuselage parts, ducts, and engine casings demand precision-bent metals with minimal margin for error. CNC-controlled plate rolls are often employed to meet the strict tolerances required in this field.
Construction and Infrastructure
From curved roofing and structural steel arches to bridges and wind towers, plate rolling machines play a key role in infrastructure development. They enable the creation of unique architectural designs and support structures.
Automotive and Transportation
Buses, trains, and commercial vehicles require curved panels and enclosures. Plate rolls allow manufacturers to produce lightweight yet strong components from aluminum and high-strength steels.
Heavy Equipment and Machinery
Bulldozers, cranes, and excavators rely on rolled steel components like cylindrical arms and protective guards. Plate rolling machines form these with durability in mind.
Choosing the Right Plate Roll
Selecting the correct plate rolling machine is critical to achieving your production goals efficiently. Here are key factors to consider:
Material Type and Thickness
Different plate rolls are designed to handle various materials such as mild steel, stainless steel, aluminum, or titanium. Thicker and harder materials require machines with higher tonnage and stronger rollers.
For example, variable geometry rolls are best for very thick or high-tensile materials, while 2-roll machines may be suitable for thin sheets.
Type of Roll (2, 3, or 4-Roll)
-
Use 3-roll machines for general-purpose bending.
-
Opt for 4-roll machines when you need precision, automation, and pre-bending capability.
-
Choose 2-roll machines for high-volume, light-gauge sheet metal work.
Roll Length
The maximum roll width should match the size of the sheets you intend to bend. Oversized rolls may increase costs unnecessarily, while undersized rolls limit your capabilities.
Cone Rolling Capabilities
If your projects include making conical shapes, ensure the machine has the necessary cone-rolling attachments or features. Not all plate rolls can perform this function efficiently.
Control System (Manual vs. CNC)
Manual machines are cheaper but require skilled operators. CNC-controlled plate rolls allow for automation, increased productivity, and exact repeatability — ideal for modern production facilities.
Speed and Efficiency
Evaluate the roll speed, material feed rates, and setup times. Faster machines enhance throughput, especially in high-volume environments.
Brand and Support
Choose a reputable brand known like 1960 Seravesi for durability, after-sales support, and spare parts availability. Reliable service can significantly reduce downtime and operating costs.
Maintenance Tips for Plate Rolls
To keep your machine operating at peak performance, regular maintenance is vital. Here are a few tips:
-
Lubricate moving parts regularly to avoid wear and overheating.
-
Inspect rollers for dents, cracks, or misalignment.
-
Check hydraulic systems for leaks and maintain fluid levels.
-
Clean control panels and ensure software is updated for CNC models.
-
Replace worn bearings and seals to prevent mechanical failures.
Proactive maintenance ensures long machine life, safer operation, and consistent product quality.
Plate rolls are one of the most essential machines in modern metalworking and fabrication. Their ability to transform flat sheet metal into precise, complex curves enables countless applications across various industries. Whether you're building pressure vessels, architectural structures, or heavy machinery components, a plate roll can be a game-changer in your production line.
From understanding how they work to choosing the right type for your needs, investing in the right plate rolling machine — and maintaining it well — will pay off in accuracy, efficiency, and profitability.
Frequently Asked Questions (FAQs)
Can a plate roll handle different metals?
Yes, most plate rolls can handle steel, stainless steel, aluminum, and more. However, machine capacity must match the material type and thickness.
What is pre-bending in plate rolling?
Pre-bending reduces the flat area at the end of the plate to achieve a consistent curve across the entire length.
How long does a plate roll machine last?
With regular maintenance, a high-quality plate roll can last 15–30 years or more, depending on usage and workload.
Do I need a CNC plate roll for small batches?
Not necessarily. For low-volume or simple jobs, manual or hydraulic machines may be sufficient. CNC adds value for complex, repetitive tasks.